LSR
THP
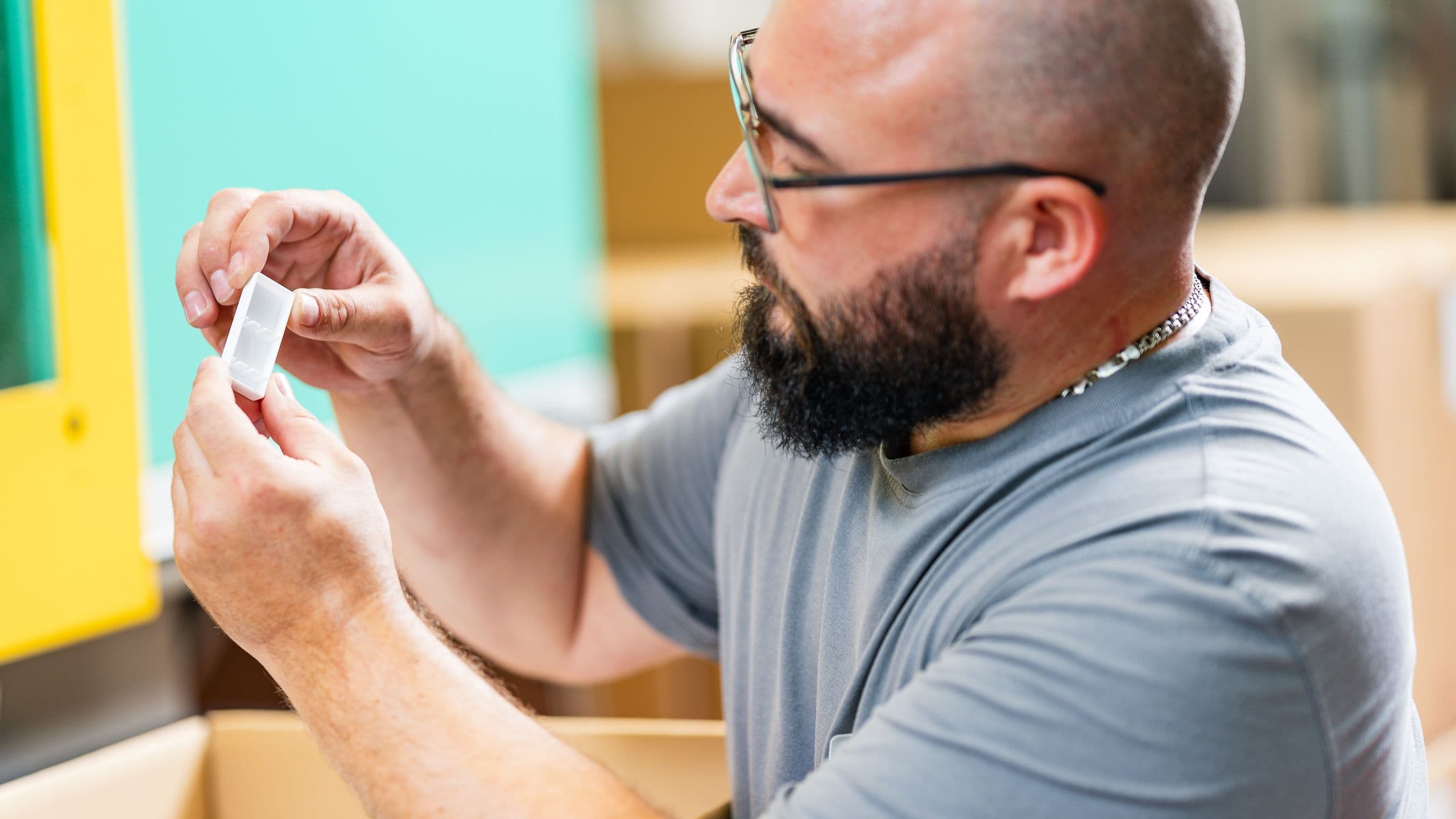
LSR and THP - High-quality materials for precise applications
Introduction to LSR and THP
LSR (liquid silicone rubber) and THP (thermoplastics) are two essential materials in modern manufacturing. While LSR impresses with its temperature resistance, dimensional stability and elasticity, thermoplastics are characterised by their high mechanical properties, component design and recyclability. Both materials offer customised solutions for different industries and applications.
Material properties
LSR is characterised by its flexibility, chemical resistance and durability, making it ideal for demanding applications in medical technology, electronics and the automotive industry. Thermoplastics, on the other hand, offer good mechanical properties, easy processing and economic and technological advantages, making them the preferred choice for packaging, technical components and household products.
Processing method
In LSR injection moulding, the silicone is injected into the cavity in liquid form and quickly cross-linked by temperature. This process enables high-precision and repeatable moulded parts. In thermoplastic injection moulding, the material is heated to the thermoplastic range, injected into the cavity and solidified by cooling. The injection moulding machines are similar in principle, the only difference being that the injection unit is cooled in the LSR and heated in the THP.
Areas of application
Thanks to their broad range of properties, LSR and THP have a wide variety of applications. LSR is used in particular for medical products, seals and electronic components, while thermoplastics are used for packaging, household goods and even technical components. The choice of the right material depends on the specific requirements of the respective application.
Take advantage of our expertise in LSR and THP injection moulding to create customised solutions for your products. Contact us for a personalised consultation!